
I finally found a guy with a machine shop that agreed to hone the spindles for me. I had one machine shop tell me that they wouldn’t do it because it was too much of a liability. Only to call the recommended shop to find out that they couldn’t do it or didn’t want to do it. Each shop either was a dead end “no” or they would tell me somebody else that “could” do it. I must have called 15 different shops trying to find one that could/would take on the job. Haha, it sounds like we are going through this together. This will give a linear bushing/bearing height and keep the pins tight for decades, as long as you keep the bushings properly lubricated. Any decent machine shop should be able to quickly hone your bushings. The pins/bushings are about the same size as typical wrist pin diameters. I highly recommend saving yourself the trouble and have the bushings properly align bore honed. Once the bushing opens up a bit it will open up some more and allow hammering of the bushing which is just a vicious cycle of beating the crap out of the bushing and making it sloppy again. Grease, or any other lubricant, will not fill these voids and support the pin.

What happens is the high spots will wear down faster(since there isn't a uniform depth) which makes the bearings wear out faster. This leaves high and low spots in the bearing surface. Also that buildup of material eventually gives way and leaves a blob and step in the cut material. If you will note, at the tip of the cutting blade there is a buildup of material and the blade itself isn't cutting, it acts more like a wedge and the material peels away. It's like watching someone cut and peel fudge. If you have ever watched a flat blade remove material from metal using a microscope you will see that the blade is more peeling the unwanted material away. It tears at the bushing material which can leave low spots. However, reaming in itself is a bit destructive to the bushing. Original Ford reamers will be long enough to fit into the opposite bushing to keep the reamer aligned in use. Only use a reamer if it is the correct Ford spec'd tool. I have heard everyone lately having same problem and DJM just tells them to tighten up the lock pin and all is good.Horse ****!!!!!!!!!!!!!!! I am going to see if I can find a machine shop to put some sleeves in mine to make the king pins fit better. I have had mine several years so I know I can't get my money back. I have the same problem with mine,and yes the dumb ass at DJM told me the same thing.
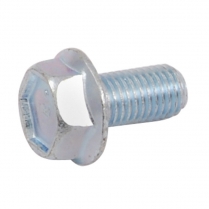
Decided to just run it stock height and have a safe truck rather than an unsafe lowered truck.

I called DJM and they advised me that the slop would go away once you crank down the wedge. He could over size them and sleeve them to the tune of a couple hundred dollars but recommended I send them back and request another set. The shop that reamed my bushings said that they wouldn't even recommend running them with as much slop as they had. My factory beams had a nice "machine" fit and the DJM had 0.050 slop. Try putting the king pin in the end of the DJM beam and check how much play you have. Trickf100 wrote:I bought and sent back a set of DJM beams because of this same problem.
